Superconductors and their potential for factory and process automation
The use of superconductors in the industrial automation sector is still in the development stage. Yet even today, completely new and efficient processes are conceivable with the technology. There is huge potential wherever contactless bearing or handling is called for – for example due to cleaning aspects, when there is spatial separation or when dealing with sensitive objects. Festo’s aim, together with evico and partners from science, is to advance the research of superconductors for industrial use and to continually develop the technology.
Festo has demonstrate three new possible applications at the Hannover Messe 2016: the contactless transfer of hovering support plates in the horizontal plane, mechanical gripping with spatial separation and the movement of an object in an enclosed tube.
SupraMotion 2016 once again demonstrates the fascinating properties of superconductors. If they are cooled down to a certain temperature, they can freeze the field of a permanent magnet at a defined distance, meaning that either they themselves or the magnet hover. The hover gap always remains stable in any spatial plane. This phenomenon enables objects to be held in position and moved without contact – with low power consumption and completely without control technology.
In the case of the SupraGripper, two grippers each with three fingers hover freely above two crescent-shaped plates. The hovering effect is achieved by the three cryostats, which are fitted underneath the plates and can be moved up and down with electrical cylinders. This means the grippers either hover above the plates or are placed onto them. In addition, the two plates can be rotated and accurately positioned with the help of two rotary drives, meaning that the two grippers can be transported from one cryostat to the next. Five CMMO-ST controllers control the cylinders as well as the rotary drives here. They feature the latest communication technology such as Ethernet or IO-link and receive their data from the Festo cloud, which enables them to be put into operation quickly.
At the start, two conventional grippers transfer one object each to the two hovering grippers. In order to grip it, electric coils on top of the cryostats give off an electrical impulse. This releases the saved connection to the magnetic gripper elements or restores it, making the individual finger elements turn up or down and the grippers open or close.
Possible applications and potential uses
The spatial separation of the magnetic gripper and superconductive drive opens up completely new solutions for harsh to extremely clean environments – for example in the pharmaceutical and chemical industry, laboratory automation and medical technology.
The electrical impulse used to open and close the fingers enables contactless mechanical gripping through an enclosed surface and even in enclosed spaces. Gripping and transferring products together with the gripping system would also be conceivable beyond the limits of the handling system. In place of the two rotary tables, a conveyor belt could run underneath the application. This would allow – depending on requirements – control of whether the gripper or goods gripped should be transported at the same time.
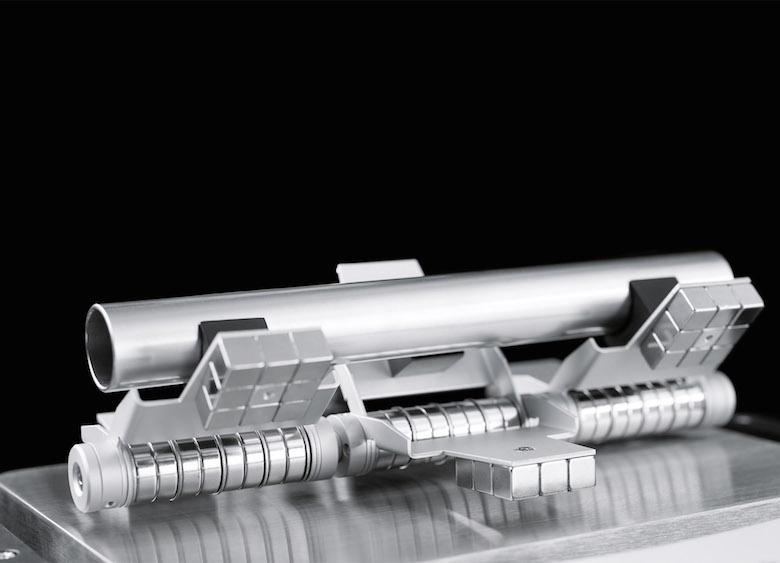
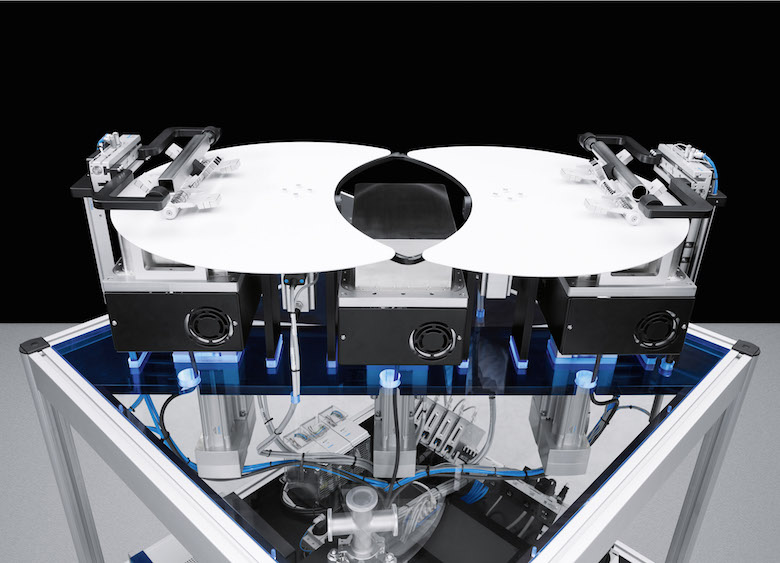